Hydraulic Engine Costs Explained Simply
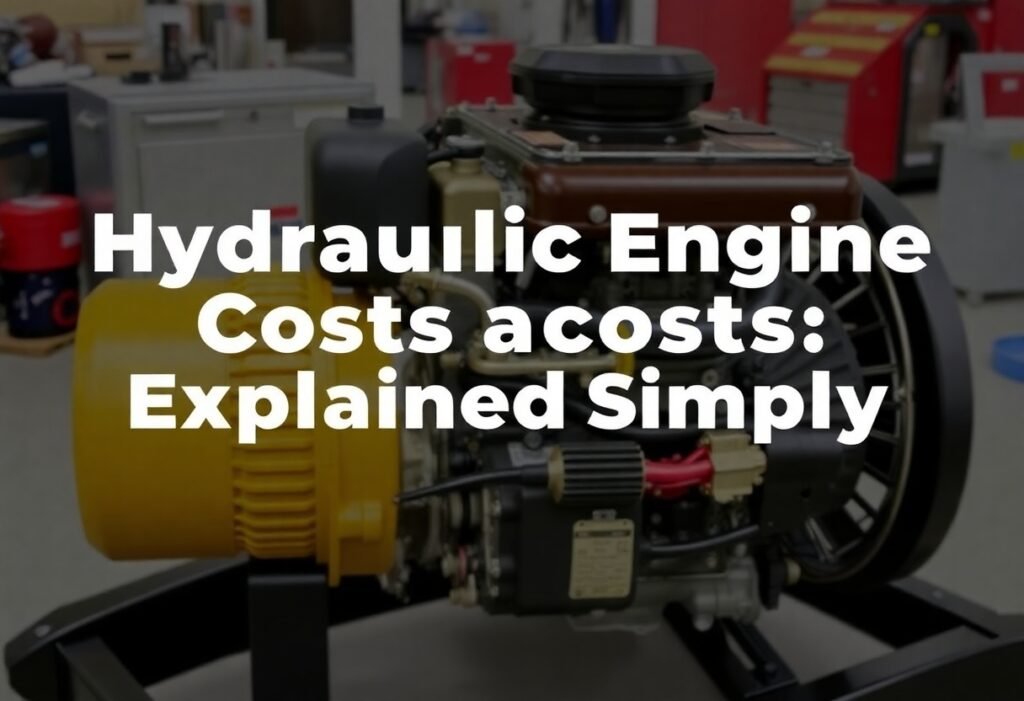
An analysis of the expenses which comprise Hydraulic Engine systems is sometimes a rather challenging task to comprehend, primarily due to the wide range of aspects, which needs to be addressed. Yet the moment the person tries to dissect the cost related with it in a step-by-step manner, the situation looks very different. Regardless of your interest in Hydraulic Engine for industrial machines, farming machinery, or some other application, you need to know the high-end costs. The indicated Systems, which are efficient, powerful and reliable may be able to deliver their value propositions with respect to costs in the long run if the costs are viewed from a system life cycle cost perspective.
Below, we’ll explore the different categories of expenses related to Hydraulic Engine Costs to help you make informed decisions.
1. Initial Purchase Costs
The first and most apparent cost to consider when investing in a Hydraulic Engine is the initial purchase price. This cost can vary widely depending on several factors:
- Size and Capacity: Bigger, high rating hydraulic engines for industrial uses will cost more than small hydraulic engines for light duties. Hydraulic systems for using in the heavy track vehicles like excavators can take tens of thousands dollars while hydraulic systems which are used in less weight applications can cost $2000 to $10000\.
- Brand and Manufacturer: Established brands often charge a premium, but they typically offer better durability, longer warranties, and more reliable support. New entrants in the market may offer lower prices but require careful consideration regarding quality.
- Custom vs. Standard Models: While standard Hydraulic Engines are relatively affordable, custom-built engines designed to meet specific application requirements may significantly increase costs. Tailored hydraulic systems can cost up to 30–50% more than off-the-shelf models.
Additional Considerations
The concern, then, when coming up with the initial cost, should not only be the expense but also the future revenue generation or return on investment (ROI). While low-cost systems seem like a better solution in the long run it can lead to high maintenance costs. It is honorable to seek quality and many a time when you are willing to pay a few pennies extra in the beginning the end result you get is far better and the equipment lasts longer.
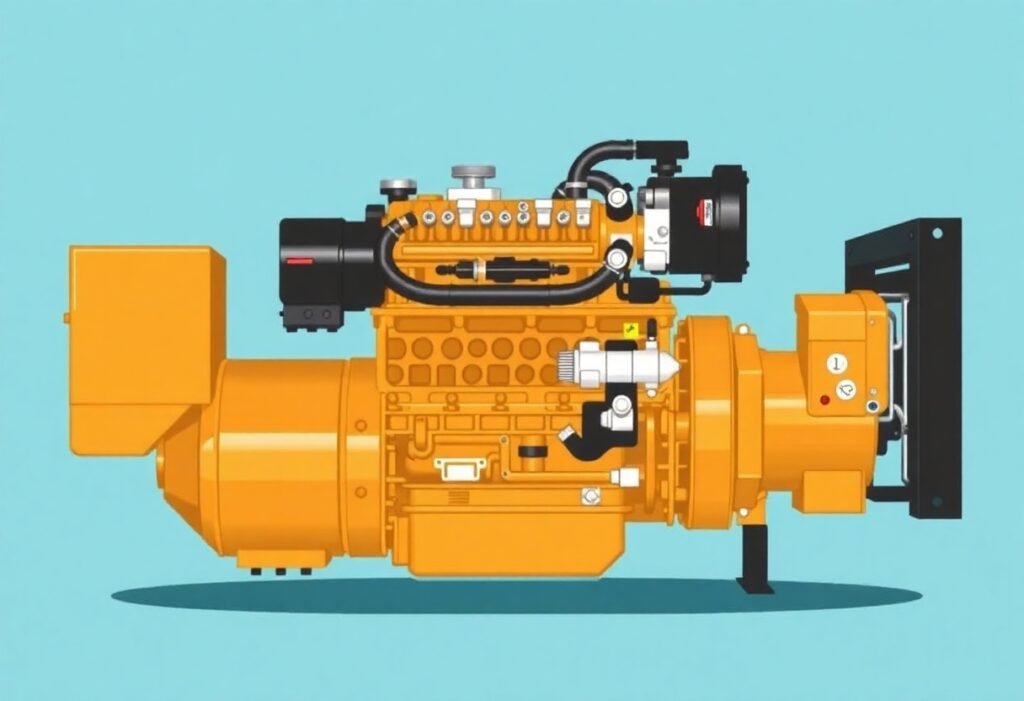
2. Installation Costs
Once a Hydraulic Engine is purchased, it doesn’t operate out of the box. Installation represents another cost category that varies based on complexity:
- System Integration: If the hydraulic system is being integrated into existing machinery, it could involve custom mounts, brackets, and connectors, which add to the expense. This is especially true if older equipment must be retrofitted to accommodate the new engine.
- Labor Costs: A professional technician or engineer is usually required to install the system correctly. Labor rates vary by location but can range between $50 to $150 per hour. Depending on the complexity, installation can take anywhere from a few hours to several days.
- Accessories and Components: Ancillary components like hoses, fittings, and filters may not always be included in the purchase price of a Hydraulic Engine. These extras can add hundreds or even thousands of dollars to the total installation cost.
3. Maintenance Costs
A significant portion of Hydraulic Engine Costs is attributable to ongoing maintenance. Like any mechanical system, hydraulic engines require regular care to operate at peak efficiency. Here’s a breakdown:
- Scheduled Servicing: Hydraulic systems typically need scheduled maintenance every 1,000 to 3,000 hours of operation. This servicing often includes fluid replacement, filter changes, and system inspections, costing anywhere from $200 to $1,000 depending on the engine size.
- Replacement Parts: Over time, moving parts will experience wear and tear. Common replacements include seals, valves, and piston pumps. Costs for replacement parts typically vary between $50 to $500, though high-end systems with specialized components can exceed $1,000.
- Hydraulic Fluid: Hydraulic fluid is essential for engine operation, and regular fluid changes are critical for preventing contamination and maintaining performance. Fluids typically cost $20 to $100 per gallon, with most systems requiring several gallons.
- Unplanned Repairs: Unexpected breakdowns can lead to costly repairs, particularly if they involve significant system failures or downtime. Regular maintenance minimizes this risk, but setting aside a contingency budget for unexpected repairs is advisable.
Cost Control Tips
Proper maintenance reduces long-term costs significantly. Monitoring fluid levels, ensuring clean filters, and conducting routine inspections can extend the life of your Hydraulic Engine, saving money over time.
4. Operational Costs
The actual cost of running a Hydraulic Engine is another factor to account for. This includes energy consumption and other operational aspects:
- Energy Costs: Hydraulic systems require energy to operate, whether it’s supplied by an electric motor, internal combustion engine, or another source. The size and capacity of the engine will directly impact energy consumption. For instance, larger systems often consume more power, contributing to higher monthly utility bills or fuel expenses.
- Efficiency Considerations: Hydraulics are known for their efficiency, often outperforming other mechanical systems in terms of energy usage. Investing in a high-efficiency model can reduce operating costs over time. Look for engines with advanced energy-saving features to further cut expenses.
- Training Costs: Proper operation also requires trained personnel. Training costs can range from a few hundred to several thousand dollars but are a crucial investment to prevent misuse that could cause mechanical damage or inefficiencies.
5. Long-Term Savings and Benefits
While Hydraulic Engine Costs can seem significant at first glance, it’s important to factor in their benefits and potential for long-term savings:
- Durability and Longevity: Hydraulic engines are designed to give long service. These systems require minimum intervention and if well maintained, they can serve a building for up to over 20 years less likely to call for replacement so often.
- Precision and Efficiency: Some characteristics of hydro systems are very accurate and smooth movements adding to the efficiency and productivity of the machines. Luftshows suggest that higher rates of production equate to improved cost per unit efficiency, in certain production settings.
- Minimal Downtime: Hydraulic engines show significantly less downtime during operation as compared to other mechanical operations even if they require maintenance frequently. Less time spent on either side of the system means less downtime and therefore it is accompanied by lesser disruption and cost saved for the particular sector, in the case of industries this could be a lot of money.
The Environmental Factor
Hydraulic systems compared to pneumatic are somewhat energy conserving though sometimes environmental friendly. The latest models are designed to incorporate environmentally safe biodegradable hydraulic fluids and energy conserving devices, and thereby have minimum environmental influence.
Summary of Costs
To summarize, here’s a quick breakdown of Hydraulic Engine Costs across various categories:
- Initial Purchase Costs: $2,000 to $50,000+
- Installation Costs: Varies widely based on complexity
- Maintenance Costs: $200 to $1,000 per servicing, plus repair contingencies
- Operational Costs: Energy and fuel costs depend on system specifications
- Training Costs: $500 to $5,000 (one-time)
In addition to the fact that each category accumulates to the total expense, such investments allow the utilization of a near-perfect and utterly dependable technology with capability of superior performance in the years ahead.
Choosing the Right Hydraulic Engine for Your Needs
In organizing, analyzing and interpreting Hydraulic Engine Costs, one must ask how the system under consideration fits into one’s own hydraulic needs. What is perquisite for you as a consumer you want high power output, long life duration or low cost? Thus when you know your needs you are able to look for the system that yields the greatest value. It is also advised that one consults industry specialists to determine costs and use of appropriate systems.
Let me put it this simply: by following a rational decision-making process the regular costs linked to your purchase will be clear to you and thus you will be making a sound investment. Today’s Hydraulic Systems and Engined remain to revolutionize industries across the globe with infinite dependability and performance across various applications.